Cotter joints are vital in mechanical engineering for connecting rods under tension or compression. They combine simplicity with practicality, making them ideal for various applications. This article delves into cotter joints, covering their parts, types, advantages, disadvantages, and practical uses.
Discover the importance of cotter joints in engineering. These simple yet effective connections are found in everything from steam engines to agricultural machinery.
Learn about their components, types, benefits, and drawbacks, and see how they play a crucial role across industries.
What is Cotter Joint?
A cotter joint is a mechanical device used to connect two rods that are subjected to axial forces like tension or compression. It is mainly used when there is a need for a detachable connection between two components.
The joint uses a flat, wedge-shaped piece of metal called a cotter, which is inserted into matching slots in the rods to hold them together securely. The design of the cotter joint consists of three main parts: the socket, the spigot, and the cotter.
The socket is usually a hollow cylinder attached to one of the rods. The spigot is a cylindrical piece on the second rod, fitting into the socket. A slot is made through both the spigot and socket, and the cotter pin is driven through this slot to secure the connection.
Cotter joints are commonly used in machines like steam engines, pumps, and heavy-duty equipment where quick assembly and disassembly of parts are required. The joint is simple in design and easy to maintain, making it a preferred choice in many industries.
It allows for the transmission of axial force while keeping the two rods tightly connected. However, it is not suitable for rotating parts due to the risk of loosening during rotation.
Cotter Joint Components
A cotter joint consists of three main components that work together to create a secure connection between two rods. These components are essential for the joint’s functionality.
1. Spigot:
The spigot is a cylindrical part attached to one of the rods. It fits into the socket of the other rod. The spigot has a slot cut through it, allowing the cotter to pass through and lock the connection.
2. Socket:
The socket is the hollow cylindrical part attached to the second rod. It houses the spigot and provides the base for the connection. Like the spigot, the socket also has a slot through which the cotter passes.
3. Cotter:
The cotter is a flat, wedge-shaped piece of metal inserted through the aligned slots in both the spigot and the socket. It holds the connection tightly by locking both parts in place. The cotter is the key component that ensures the rods remain securely joined.
Types of Cotter Joints
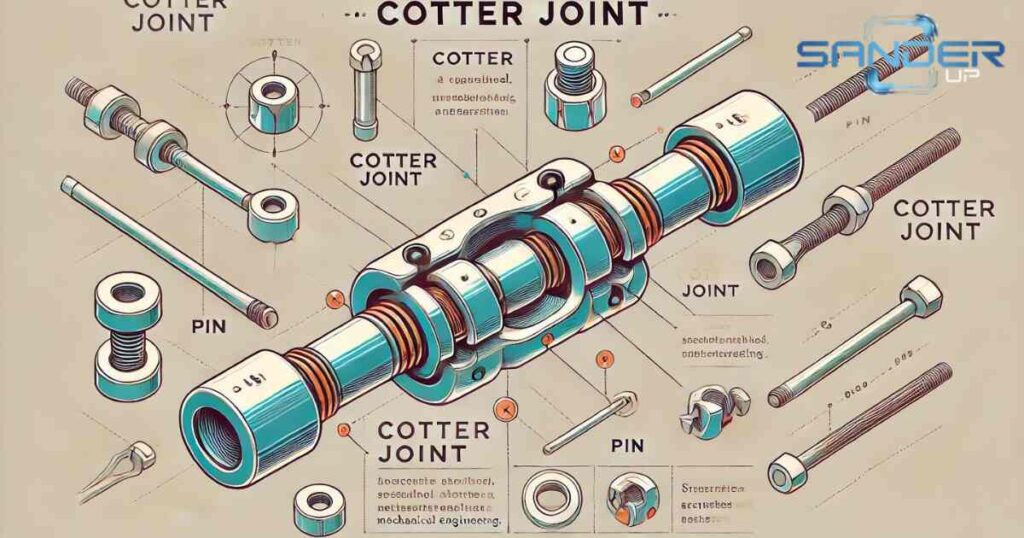
Cotter joints come in different types depending on the design and application requirements. Each type is suited for specific kinds of mechanical connections and load conditions. Below are the three primary types of cotter joints.
1. Socket and Spigot Cotter Joint:
This is the most commonly used type of cotter joint. In this design, one rod has a cylindrical end known as the spigot, while the other rod has a hollow cylindrical end called the socket. The spigot fits into the socket, creating a connection between the two rods.
Both the spigot and socket have aligned slots, and the cotter is inserted through these slots. The cotter locks the rods together, allowing the joint to transmit axial force.
This type of cotter joint is widely used in mechanical applications where axial loads, such as tensile or compressive forces, need to be transmitted between two rods. It is simple in construction and allows for easy assembly and disassembly. It is frequently used in piston rods, connecting rods, and steam engines.
2. Sleeve and Cotter Joint:
In a sleeve and cotter joint, both rods to be connected are inserted into a common cylindrical sleeve. The sleeve acts as an outer casing, and both rods are slotted. The cotter is passed through the sleeve and both rods, securing them together.
This type of cotter joint is preferred when larger rods are involved, or when axial force needs to be transmitted between rods of different diameters.
The sleeve provides additional support and increases the strength of the connection, helping to prevent issues like undercut in welds. It is often used in heavy machinery where large forces are transmitted, such as in construction equipment.
3. Gib and Cotter Joint:
The gib and cotter joint is a variation of the socket and spigot type, with the addition of a gib. The gib is a tapered piece that is inserted alongside the cotter.
It serves to prevent the cotter from loosening during operation. The gib also helps in distributing the load more evenly across the joint, increasing its strength.This type of joint is used when the connection needs to handle higher loads or when the forces on the joint are not purely axial.
The addition of the gib provides extra security against the cotter loosening and ensures a more durable and reliable connection. Gib and cotter joints are often found in heavy-duty applications such as cranes, lifting machines, and engines, where the joint must withstand large forces.
Failure of Cotter Joints
Cotter joints can fail due to several factors, often related to design, material, or usage conditions. Understanding these failure modes is crucial for ensuring reliability and safety in applications.
- Shear Failure:
This occurs when the cotter pin experiences excessive shear stress, leading to its breakage. If the applied load exceeds the cotter’s shear strength, it may snap, causing the joint to become loose or disconnect entirely.
- Tensile Failure:
In cases where the joint is subjected to high tensile loads, the rods or the cotter may experience tensile failure. This happens when the material reaches its ultimate tensile strength, resulting in stretching or breaking.
- Fatigue Failure:
Repeated loading and unloading cycles can lead to fatigue failure. Over time, micro-cracks develop in the cotter or the rods due to cyclic stresses. Eventually, these cracks can grow large enough to cause complete failure.
- Corrosion:
Corrosion can weaken the material of the cotter joint, particularly if it is exposed to harsh environments. Rust or chemical degradation can lead to a reduction in strength, making the joint more susceptible to failure.
- Improper Installation:
Incorrect installation, such as misalignment or insufficient tightness of the cotter pin, can lead to premature failure. Ensuring proper alignment and securing the cotter correctly is essential for the joint’s integrity.
Advantages of Cotter Joints
Cotter joints offer several benefits that make them a popular choice in mechanical applications. Here are some of the key advantages:
Simple Design:
Cotter joints have a straightforward design, consisting of basic components like the spigot, socket, and cotter. This simplicity makes them easy to manufacture, assemble, and disassemble.
Detachable Connection:
One of the significant advantages of cotter joints is their ability to create a detachable connection. This feature allows for easy maintenance and replacement of parts without requiring complex procedures.
Cost-Effective:
The materials used in cotter joints are typically low-cost, and their simple design contributes to reduced manufacturing costs. This makes cotter joints an economical choice for many applications.
Versatility:
Cotter joints can be used in a wide range of applications, from small machinery to large industrial equipment. They are suitable for connecting rods in various configurations and load conditions.
Effective Load Transmission:
Cotter joints are designed to transmit axial loads effectively. They can handle both tensile and compressive forces, making them reliable in applications where such loads are present.
Easy Maintenance:
Due to their simple design and detachable nature, cotter joints are easy to inspect and maintain. Any wear or damage can be quickly identified and repaired without significant downtime.
Space Efficient:
Cotter joints require minimal space compared to other types of joints. This makes them suitable for applications where space is limited, such as in compact machinery.
Disadvantages of Cotter Joints
- Cotter joints may have limited strength compared to other types of joints, making them less suitable for high-load applications.
- They can be prone to shear failure if subjected to excessive forces, which can lead to sudden joint failure.
- Over time, repeated loading can cause fatigue in the cotter, leading to the development of cracks and eventual failure.
- Misalignment during installation can lead to uneven load distribution, increasing the risk of premature wear and failure.
- Corrosion and wear due to environmental factors can weaken the cotter or rods, compromising the joint’s integrity.
- The cotter can loosen over time, especially under dynamic loading conditions, necessitating regular maintenance to ensure a secure connection.
- They may not be suitable for rotating applications due to the risk of the cotter pin coming loose during rotation.
Cotter Joints Application
- Cotter joints are commonly used in connecting piston rods to crossheads in steam engines and hydraulic cylinders, allowing for effective load transmission and easy maintenance.
- They are found in machinery like pumps and compressors, where a detachable connection is needed for maintenance without disrupting the entire system.
- In construction equipment, cotter joints connect various structural components, ensuring robust performance under heavy loads.
- Cotter joints are often utilized in automotive applications, such as in the suspension system, where they help link various parts while allowing for adjustments.
- They are used in agricultural machinery, like tractors and harvesters, to connect rods and links that require frequent maintenance or replacement.
- Cotter joints are also found in the assembly of cranes and lifting devices, where they secure components under varying loads while allowing for quick disassembly when needed.
- In general, cotter joints are suitable for any application requiring a strong, detachable connection that can handle axial loads efficiently.
FAQ’s
What is the difference between a pin joint and a cotter joint?
A pin joint connects two parts using a pin that allows rotation. It offers flexibility and is often used in structures like bridges.
A cotter joint uses a cotter (a wedge-shaped piece) to secure the connection. It allows limited movement and is typically used in machinery for aligning components.
Pin joints allow more rotation, while cotter joints provide a more secure but less flexible connection.
Is cotter joint a permanent fastening?
No, a cotter joint is not a permanent fastening. It allows for disassembly and reassembly. The cotter can be removed easily, making it suitable for situations where parts need to be adjusted or replaced.
What are the three types of cotter pins?
There are three types of cotter pins. The split cotter pin is the most common. It has a split end that can be spread apart after it is inserted. This helps secure it in place. The tapered cotter pin has a tapered shape. This allows it to fit snugly in holes, providing a tight fit. It is often used in machinery. Finally, the locking cotter pin has a special locking mechanism. This prevents accidental removal and is used when security is important.
What is the advantage of a knuckle joint over a cotter joint?
Knuckle joints offer several advantages over cotter joints in certain applications:
- Higher Strength: Knuckle joints can handle higher loads and forces compared to cotter joints. Their design provides better resistance to shear and tensile stresses.
- Rotational Capability: Unlike cotter joints, knuckle joints allow for rotation between the connected rods. This feature is beneficial in applications where parts need to move relative to each other.
- Better Alignment: Knuckle joints can accommodate misalignment between connecting components. This flexibility helps reduce stress concentrations and the risk of failure.
- Reduced Wear: The design of knuckle joints often leads to less wear on the contacting surfaces compared to cotter joints, especially under dynamic loading conditions.
- Greater Durability: Knuckle joints tend to have a longer service life in applications involving frequent movement or varying loads, making them suitable for demanding environments.
What are the rules for cotter pins?
Cotter pins are essential for securing bolts and keeping components in place. To use them properly, choose the right size and type for your specific application, as they come in various lengths and diameters. During installation, insert the pin through the hole in the fastener, and bend the ends to secure it.
Ensure the ends are bent evenly to create a tight fit, but avoid over-bending, as this can weaken the pin. Regularly inspect cotter pins for wear or damage, replacing any that are corroded or broken. Lastly, make sure there are no sharp edges sticking out after installation to prevent injuries. Using cotter pins correctly ensures safety and function in machinery.
Why is the cotter tapered?
The cotter is tapered to provide a tight fit and secure fastening. This taper allows it to lock in place when inserted into a hole or slot, preventing movement. The design also makes it easier to remove when needed. Overall, the taper enhances stability and safety in mechanical connections.
What is a cotter pin called?
A cotter pin is also called a split pin. It is a fastener used to secure two or more components together, typically in a clevis or a pin joint.
What is the length of a cotter pin?
The length of a cotter pin can vary widely, typically ranging from 1 inch to 6 inches or more. Common lengths include 1.5 inches, 2 inches, and 3 inches. The right length depends on the application and the components being secured.