Undercut in welding can compromise the integrity of a weld, leading to potential failures. Understanding its causes and prevention methods is crucial for producing strong, reliable joints.
What is Undercut?
Undercut in welding refers to a defect that occurs along the edges of a weld. It happens when the base metal is melted away more than intended. This creates a groove or notch, weakening the joint. Undercut can lead to structural failures if not addressed.
The primary causes of undercut include improper welding technique and excessive heat. When the welder moves too quickly or uses a high amperage, the heat can erode the base material. Poor joint design can also contribute to this issue.
Preventing undercut involves careful control of the welding parameters. Welders should adjust the heat settings and travel speed. Proper preparation of the joint and selecting the right filler material can also help. Regular inspection during the welding process ensures any defects are caught early.
Addressing undercut is essential for maintaining the integrity of welded structures. If detected, it may require additional welding or grinding to fix the problem. By understanding and preventing undercut, welders can improve the quality of their work and enhance safety.
Types of Undercut
Undercuts are specific haircuts that create a stark contrast between different hair lengths. They can be categorized into two main types: external and internal undercuts.
External Undercut
An external undercut involves shaving or cutting the hair on the sides and back while leaving the top longer. This style creates a dramatic contrast. It is popular for its bold look and versatility. People often style the longer hair in various ways, from slicked back to messy.
Internal Undercut
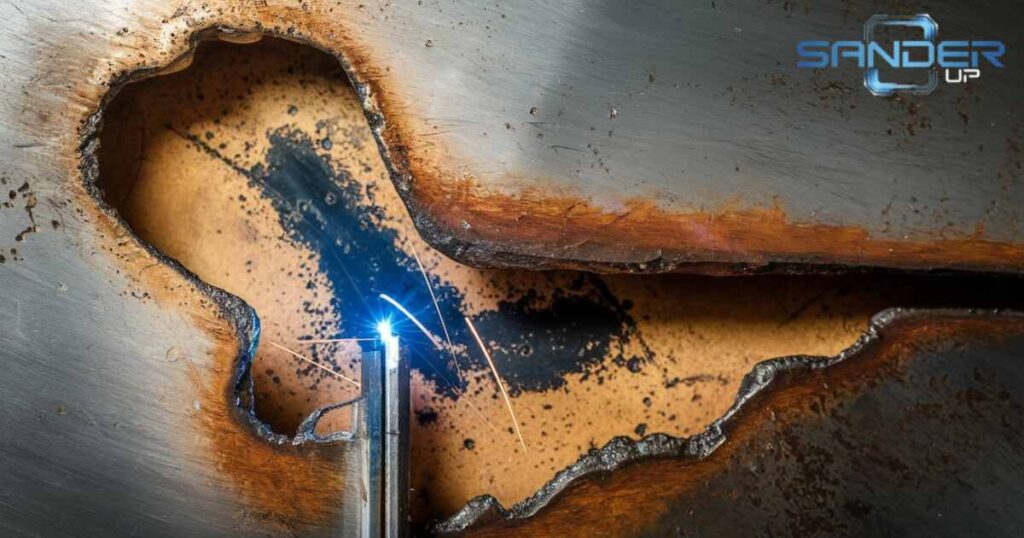
An internal undercut is less visible. It features shorter layers hidden beneath longer hair. This style gives a subtle edge without the bold contrast of an external undercut. It’s ideal for those who want a unique look without being too drastic. This option is also versatile, allowing for different styles on top while keeping the undercut discreet.
How to Prevent Undercutting?
Undercutting in welding is a common issue that can weaken the weld joint. Here are some effective ways to prevent it.
Choosing the Right Welding Technique
The choice of welding technique can significantly impact the occurrence of undercutting.
TIG Welding
TIG welding offers better control over heat and material flow. It produces high-quality welds with minimal undercutting when done correctly.
Stick Welding
Stick welding can also prevent undercutting if the right electrode is chosen. Proper technique and movement are crucial to avoid excessive melting of the base metal.
MIG Welding
MIG welding is efficient for preventing undercutting. It provides a steady arc and good penetration, reducing the risk when using the correct settings.
Adjusting Welding Parameters
Properly adjusting welding parameters is essential for preventing undercutting.
Right Amperage Proper Voltage
Using the correct amperage ensures the right heat input. Too high can lead to undercutting. Voltage affects the arc length. Maintaining the right voltage helps achieve good fusion without excessive melting.
Appropriate Travel Speed
Moving too quickly can cause undercutting. The speed should allow proper heat distribution.
Skilled Handling of the Torch, Electrode Holder, “Stinger,” or MIG Gun
Skilled handling is key. Proper technique prevents excessive heat in specific areas, which can cause undercutting.
Using Proper Equipment and Tools
Using the right equipment and tools is vital in preventing undercutting.
Electrode & Shielding
The choice of electrode and shielding is crucial in welding. Proper selection helps ensure strong welds while preventing defects like undercuts. Here are key considerations for electrodes and shielding:
Improper Electrode Material
Using the wrong electrode material can lead to poor weld quality. Different materials require specific electrodes for optimal bonding. Ensure that the electrode matches the base metal type. This compatibility is essential for achieving a strong weld and preventing issues like undercuts.
Electrode Angle
The angle of the electrode during welding affects the heat distribution. An incorrect angle can lead to improper fusion. Ideally, maintain a 10 to 15-degree angle from vertical. This helps direct the arc efficiently, reducing the risk of undercuts and ensuring better penetration.
Wrong Electrode Size
Using an inappropriate electrode size can create problems. An electrode that is too small may not provide enough heat, leading to weak joints. Conversely, a larger electrode can cause excess heat, resulting in undercuts. Always choose an electrode size suitable for the thickness of the material being welded.
Incompatible Shielding Gas
The choice of shielding gas is vital in protecting the weld pool. Using an incompatible gas can lead to oxidation and contamination. Ensure the shielding gas matches the electrode and base material. This compatibility promotes a clean weld and minimizes defects like undercuts.
Prevention Checks for Undercutting in Automated Welding
Undercutting in automated welding can weaken joints and affect structural integrity. To prevent this issue, specific checks and practices should be followed.
Setting and Checking Machine Parameters
Setting the correct machine parameters is crucial. This includes adjusting voltage, current, and travel speed. Each material type requires different settings. Regularly check these parameters before starting a project. Use test welds to verify that settings produce the desired results. Keeping a log of adjustments can help maintain consistency over time.
Proper Maintenance and Calibration of Welding Machines
Regular maintenance of welding machines is essential. Ensure machines are clean and free from debris. Check for wear and tear on components like nozzles and tips. Calibration should be performed periodically to ensure accuracy. Following manufacturer guidelines for maintenance can extend the life of the equipment and improve performance. Regular checks can help identify potential issues before they lead to undercutting.
What is the Acceptable Amount of Undercut?
The acceptable amount of undercut in welding depends on several factors, including the type of weld and the material used. Generally, guidelines specify limits to ensure structural integrity.
Welding Standards: Many organizations, like the American Welding Society (AWS), provide standards for acceptable undercut levels. Typically, undercut should not exceed 1/32 inch (0.8 mm) for most applications.
Material Type: Different materials have varying tolerances. For instance, aluminum may allow for less undercut compared to steel due to its lower strength.
Weld Type: The type of weld also influences acceptability. Fillet welds may tolerate slightly more undercut than groove welds.
Inspection Methods: Visual inspections and non-destructive testing (NDT) are used to assess undercut. Any undercut beyond acceptable limits may require rework or repair.
Safety Considerations: Always prioritize safety and structural integrity. If there’s any doubt, consult industry standards or a welding engineer for guidance.
3 Main Causes of Undercut
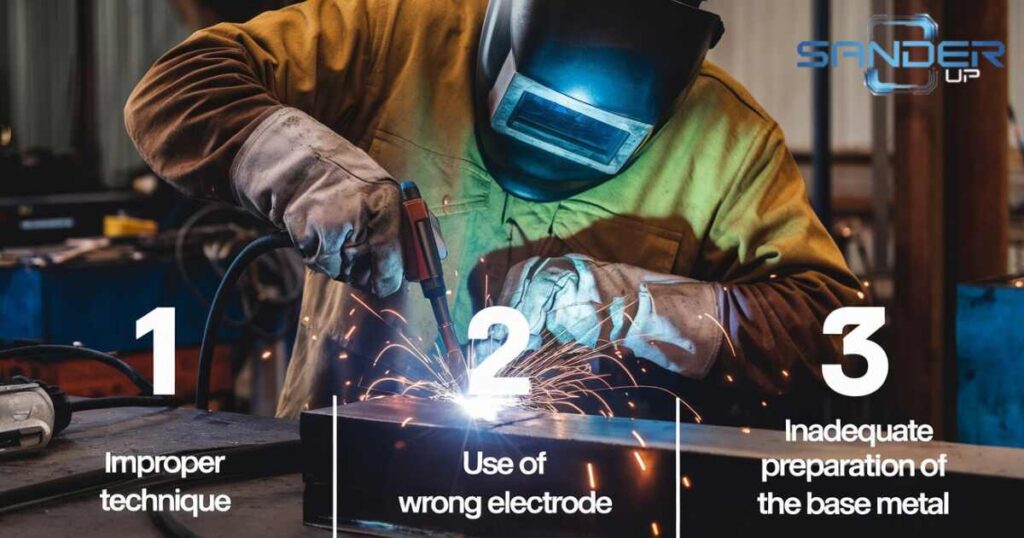
Understanding the causes of undercuts is essential for welders aiming to produce high-quality welds. Here are the three main causes, explained in detail:
1. Wrong Welding Parameters
Incorrect welding parameters can lead to significant issues, including undercuts.
High Current
Using too high a current can result in excessive heat input, leading to an overly fluid weld pool. When the weld pool becomes too shallow, it fails to penetrate adequately into the base material. This creates a weak joint prone to undercuts. Maintaining the correct current is crucial for achieving a stable and strong weld.
High Travel Speed
If the welder moves too quickly, the weld pool doesn’t have enough time to fuse properly with the base material. This can create an inadequate bond and lead to undercuts along the edges. A consistent travel speed allows for even heat distribution, promoting better penetration and a stronger weld.
High Arc Voltage
High arc voltage can destabilize the weld pool, making it more difficult for the molten metal to adhere to the base material. This instability can cause the weld metal to retract from the edges, leading to undercuts. Keeping the voltage at the correct level is essential to ensure a smooth and even weld.
2. Wrong Electrode & Shielding Gas
The choice of electrode and shielding gas is vital for preventing undercuts.
Improper Electrode Material
Using an electrode that does not match the base metal can result in poor bonding. If the materials are incompatible, the weld may not fuse properly, leading to undercuts. Selecting the appropriate electrode material for the specific job ensures a strong and reliable weld.
Electrode Angle
The angle of the electrode affects how the heat is applied to the weld. If the electrode is not angled correctly, it may direct the arc away from the joint, preventing proper fusion. Maintaining an angle of 10 to 15 degrees is recommended to achieve optimal penetration and minimize the risk of undercuts.
Wrong Electrode Size
Choosing an electrode that is too large or too small can also lead to undercuts. An oversized electrode may create excessive heat, while an undersized one might not provide enough filler material for adequate fusion. Selecting the right size ensures the weld has sufficient strength and minimizes the chances of undercutting.
Wrong Shielding Gas
The type of shielding gas used can impact the weld’s integrity. If the gas does not effectively protect the weld pool from atmospheric contamination, it can lead to oxidation and other issues. Using the right shielding gas helps maintain a stable arc and ensures a clean weld, reducing the likelihood of undercuts.
3. Wrong Welding Technique
Welding technique plays a crucial role in preventing undercuts.
Weaving Technique
A poor weaving technique can lead to uneven heat distribution. If the welder does not control the weaving motion well, it can create weak points in the weld. Proper weaving ensures that heat is applied consistently, allowing for better penetration and reducing the risk of undercuts.
Excessive Arc Length
Maintaining an excessive arc length can prevent proper fusion between the weld and base material. When the arc length is too long, the heat is not concentrated enough to melt the base metal adequately. Keeping a shorter arc length ensures that the weld pool is stable and penetrates effectively.
Lack of Edge Preparation
If the edges of the base material are not prepared correctly, it can result in poor penetration during welding. Lack of edge preparation creates a barrier that prevents the weld metal from adhering properly to the base material. Proper edge preparation is essential for achieving a strong bond and minimizing the chances of undercuts.
Removing Undercuts for a Bad Weld
Undercuts in welding can lead to weak joints. They occur when the weld metal does not fuse properly with the base metal. This can happen due to improper technique or settings. Removing these undercuts is crucial to ensure the integrity of the weld.
To start, identify the areas with undercuts. Use a grinder or a rotary tool to remove the bad weld. Ensure you remove enough material to eliminate the undercut completely. Take care not to damage the surrounding area.
Once the undercuts are removed, clean the surface thoroughly. Remove any debris, dust, or oils. This prepares the surface for re-welding.
Next, reapply the weld in the affected area. Use proper settings and techniques to avoid future undercuts. After re-welding, inspect the joint closely. A good weld should have smooth transitions without any visible undercuts.
Finally, consider using a grinder or file to finish the weld. This helps achieve a smooth surface. Proper finishing not only improves appearance but also ensures the strength of the weld.
10 Quick Tips to Prevent Undercut in Welding
Preventing undercuts is essential for strong welds. Here are ten quick tips to help you avoid this common issue:
- Adjust the Travel Speed: Move at a steady pace. Too fast can cause undercuts, while too slow may lead to excessive heat.
- Set Proper Voltage: Ensure the voltage is appropriate for the material and thickness. High voltage can contribute to undercuts.
- Use Correct Electrode Angle: Keep the electrode at a 10 to 15-degree angle. This helps direct the arc properly and prevents undercuts.
- Maintain Proper Arc Length: A shorter arc length can reduce undercuts. Keep the electrode close to the workpiece without touching it.
- Clean the Workpiece: Remove contaminants like rust, paint, or oil. A clean surface promotes better weld penetration.
- Use Backing Bars: Employ backing bars or blocks to support the weld. This helps reduce undercutting at the edges.
- Control Heat Input: Avoid overheating the base material. Excessive heat can cause melting and result in undercuts.
- Select the Right Filler Material: Use filler materials compatible with the base metal. This ensures a strong bond without undercuts.
- Practice Good Technique: Regularly practice welding techniques. Good habits can prevent undercuts and improve overall weld quality.
- Inspect and Adjust: Regularly inspect your welds. If you notice undercuts, adjust your technique and settings accordingly.
Can You Fix Undercuts in Welding?
Yes, you can fix undercuts in welding, and it’s important for weld integrity. Start by identifying the undercut areas and use a grinder to remove them completely, being careful not to damage the surrounding metal.
After that, clean the area thoroughly to eliminate any debris or contaminants. Reapply the weld using the correct technique and settings to ensure proper penetration.
Finally, inspect the repaired weld for quality, ensuring there are no visible undercuts. A good repair enhances both the appearance and strength of the weld.
What Are the Main Effects of Having Undercuts in Your Weld?
Undercuts can significantly impact the quality and integrity of a weld. Understanding these effects is crucial for welders.
First, undercuts weaken the weld joint. They create notches that can lead to stress concentration. This increases the likelihood of failure under load, compromising the entire structure.
Second, undercuts can cause fatigue issues. Repeated stress can lead to cracks developing in the weak areas. This can result in premature failure, especially in critical applications.
Third, they may affect the appearance of the weld. Aesthetic quality is important in many projects. Undercuts create an uneven surface, which may not meet visual standards.
Undercuts can complicate further processing. If additional welding or finishing is needed, it becomes challenging to achieve a smooth, even surface.
Finally, undetected undercuts can lead to safety hazards. Instructive welds, such as those in structural applications, must be reliable. Undercuts pose a risk that could lead to catastrophic failures.
Addressing undercuts is essential for ensuring strong, reliable, and safe welds. Regular inspection and proper technique can help prevent these issues.
FAQ’s
Why is undercut harmful to a weld?
Undercut in a weld is harmful because it creates a groove along the edge of the weld. This weakens the joint by reducing its cross-sectional area, making it more susceptible to failure under stress. Undercut can also lead to stress concentration points, increasing the risk of cracking or fatigue over time. Overall, it compromises the integrity and strength of the weld.
Can damage from an undercut be fixed?
Yes, damage from an undercut can be fixed. The process typically involves:
1. Grinding: The undercut area is ground down to create a smooth surface.
2. Re-welding: After grinding, the area is filled with additional weld material to restore strength.
3. Inspection: The repair is inspected to ensure it meets quality standards.
Does undercut weaken a weld?
Yes, undercut weakens a weld. It reduces the effective cross-sectional area of the weld, making it more prone to failure under load. This can lead to cracks or structural failure over time, compromising the overall strength of the welded joint.
How much undercut is allowed in a weld?
The allowable amount of undercut in a weld depends on the welding code or standard being followed. Generally, most codes permit an undercut of about 1/32 inch (0.8 mm) or less. However, for critical applications, even less may be acceptable. Always consult the specific welding standard relevant to your project for precise limits.
What is the difference between undercut and underfill?
Undercut is a groove along the weld edges, weakening the joint. Underfill is insufficient weld material in the joint, leading to gaps and reduced strength.